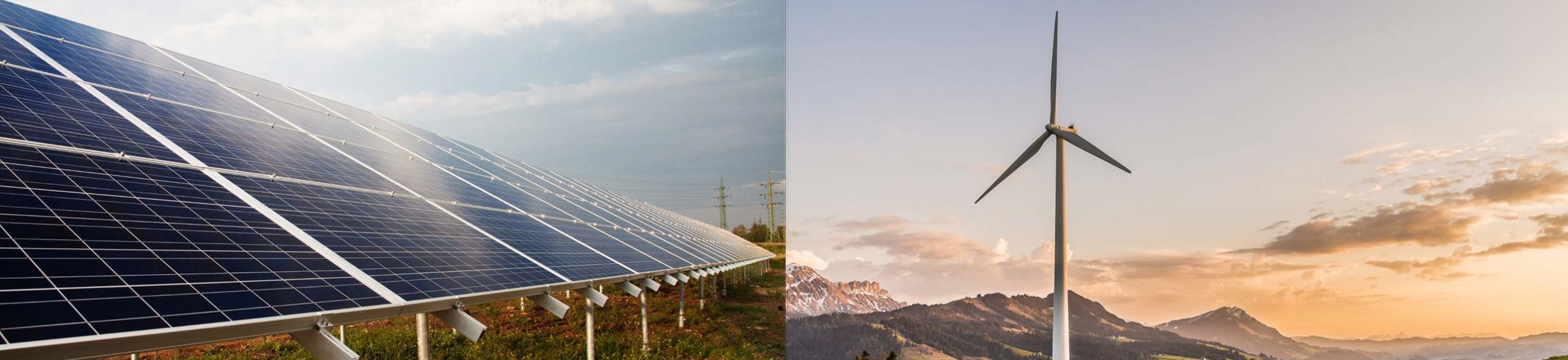
Technology
Step 1: Dewatering from 0.001% up to 35% TS
This is where the greatest savings potential lies, we are talking here about large volume reductions of sludge with saved costs. See what you can save under opportunities on this page.
Settlement tanks
Sedimentation is a simple and effective way to purify water. The purpose of a sedimentation tank or settling tank is to remove solid particles and sediments from the water using the force of gravity. This is a critical step in the water purification process as it helps improve water quality by reducing particle concentration and removing particles that may contain contaminants, such as organic matter, sand and silt.
Press screw
Screw presses are simple and reliable machines that are placed in the material flow where it is desirable to separate the liquid from the dry matter. Mechanical dewatering is by far the most economical method. Capacity 0.1-100m3 / hour. The frequency and solids content can be changed using a frequency converter. Screw presses are supplied with central pipe or without central pipe in screw rotor. Depending on the sludge type, screw presses can deliver dewatered sludge from 20 up to 40% TS
Belt filter
Band filter system combines three critical processes into one compact unit – dry matter separation, sludge thickening and dewatering. The endless filter cloth removes 50% TSS and> 20% BOF from the wastewater and can produce dry sludge (20% TS). It is the only filter design that can replace conventional primary treatment at comparable cleaning levels at a competitive price. The belt filter system is ecologically efficient in that it is cost-effective, compact, can operate without the use of chemicals and can thus be a sustainable solution.
Siew screw
Filtering, or draining of liquid, can be a good way of dewatering pulp. Especially if there is a lot of free water in the pulp, or it is fragile, and can not withstand pressure. Sealing can also be used in direct combination with a screw press, by providing the inlet portion of the screw with e.g. stave sieve or hole sieve.
Oval Disk dewatering
ODA is an energy efficient solid-liquid separator with self-cleaning function and high capacity. The opening between the solid and the rotating oval rings permits the liquid to pass through and push the solid further in the process. The rotation between the rings cleans the system and prevents clogging of the dried sludge. The process can be run continuously and is automated. Operator control is low and the self-cleaning function provides good flow in the separation process. The oval rotating rings transport the mud toward the outlet of the machine while separating the water from the mud. The design of the system is simple and requires little maintenance. Low rotation speed provides long running time and low maintenance costs. Compared to other dewatering systems, ODA has low energy consumption. The energy consumption varies from 0.2 kW to 1.5 kW from the smallest to the largest machine which provides from 23 to 130 m3 / hour capacity. The separator is a complete sludge dewatering system that can be adapted to most processes and industries. The system can be supplied with associated feed and feed systems, and can be operated as a continuous process.
The process can be run continuously and is automated. There is a small need for operator control and self-cleaning function provides good flow in the separation process. The oval rotating rings transport the sludge towards the outlet of the machine while separating the water from the sludge.
The system is simple to build and requires little maintenance. Low rotation speed results in long operating time and low maintenance costs. Compared to other dewatering systems, ODA has low energy consumption. Energy consumption varies from 0.2 kW to 1.5 kW from the smallest to the largest machine, which provides from 23 to 130 m3/ hour capacity.
The separator is a complete sludge dewatering system that can be adapted to most processes and industries. The system can be supplied with associated systems for feeding and discharging and can be operated as a continuous process.
Step 2: drying from 25% to 98% TS
After dewatering thin sludge to 25-35% TS, it may be useful for various reasons to remove the last part of the water for, among other things, further reducing the amount and stabilizing the sludge.
Hammer mill
The TMD (Thermo-Mechanical Dryer) technology is designed to dry materials that are difficult to dry in conventional dryers. The material is fed into a hammer mill where it is crushed into small particles while being heated directly by friction. This makes the machine ideal for treating all materials that meet the “glue phase”, without requiring dry solids recycling. Since heat is transferred by friction directly into the material, the TMD machine has a very high thermal efficiency (> 95%). Evaporated liquid is condensed and can be transported to tanks or discharges, depending on local requirements. The solids are 100% dried and dispensed in the form of fine-grained powder. The TMD machine is easy to install, fully automated and powered only by clean electricity – No oil burners or steam production are required.
Plate Dryer
Plate dryer can with its unique design and operating temperature of approx. 100 degrees Celsius is used in the process of dewatering / evaporating sludge. The sludge volume in the process is reduced from a humidity of 70% to a humidity of scarce 5 to 10%, the temperature of the process ensures that the pre-dried sludge is sterile and storage stable. The steam from the drought itself can be recovered as energy in, for example, a further evaporation process, which together with the reduction of waste volume is a very positive contribution to the environment. The size and capacity of our dryers can be adapted to the customers’ needs.
Steam Dryer
Steam dryer where sludge with a dry matter content of more than 15 percent is run through a double screw. Superheated steam of about 200 degrees does the drying itself. This excess steam passes through a heat exchanger where it is condensed and where the spent energy is partially recovered in the form of heating the cooling water. This can then be used for heating the plant.
Lime treatment (Orsa)
Wastewater produces a sludge during the precipitation and/or water treatment processes at a treatment plant. This sludge must be conditioned before dewatering, sanitised and stabilised. That is, the sludge must be treated in such a way that it easily releases the water during dewatering, does not present a risk of infection and stabilises to prevent odours. Lime can be used for two types of treatment. One method is called the Orsa method, where quick lime is added directly. The other method is conditioning where slaked lime or quick lime is added to the raw sludge before dewatering to improve the dewatering properties.
There are two forms of treatment with lime. One method is called the Orsa method, where quicklime is added directly. The second method is conditioning where hydrated lime or burnt lime is added to the raw sludge before dewatering to improve the dewatering properties.